Meta-material Design Breaks Through! Meta AI and Others Proposed UNIMATE, Which First Realized Unified Modeling of Tasks Such As Topology Generation and Performance Prediction
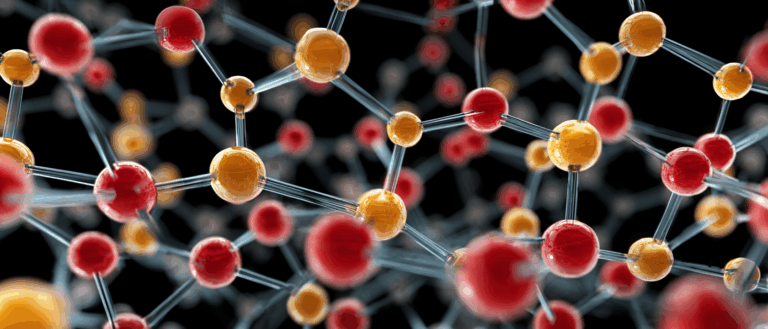
Metamaterials are a type of material composed of artificially designed subwavelength structures that can break through the inherent limitations of natural materials and achieve precise control of electromagnetic waves, such as negative refractive index, super lenses, stealth technology, etc. Among them, mechanical metamaterials, as a type of artificial material with special mechanical properties, have shown great application potential in aerospace, biomedicine, energy storage and other fields.What makes it unique is that the properties are not determined by the chemical composition of the material, but are achieved through a carefully designed microstructure.For example, metamaterials with negative Poisson's ratio expand laterally when stretched, a property that makes them valuable for use in flexible devices, while metamaterials with high energy absorption behavior are suitable for use in cushioning devices.
In the intersection of materials science and artificial intelligence, the design and optimization of metamaterials has always been a research direction that has attracted much attention.Three key modalities are usually involved: 3D topology, density conditions, and mechanical properties.There is a close relationship between these three modes. If any two of them are known, the third mode can be derived. However, the research team found through a comprehensive review of existing literature that most existing studies only consider two of the modes. For example, predicting mechanical properties given a 3D topological structure, or generating a 3D topological structure based on the required performance.This limitation makes it challenging for existing machine learning models to handle complex practical application scenarios, making it difficult to fully capture the complete relationship between the three modalities.
To fill this research gap, a research team from Virginia Tech and Meta AI proposed a unified model called UNIMATE, which for the first time built a unified framework that can handle the three major modes of metamaterial design at the same time. Through the innovative architecture of modal alignment and collaborative diffusion generation, it achieved the collaborative optimization of the three major tasks of topology generation, performance prediction, and condition confirmation. This research not only fills the technical gap in multi-task metamaterial design, but also provides a general methodology for intelligent material discovery.
The research results, titled "UNIMATE: A Unified Model for Mechanical Metamaterial Generation, Property Prediction, and Condition Confirmation", were selected for ICML 2025.
Research highlights:
* Cross-task generalization: A single model can solve three major tasks simultaneously, breaking through the task limitations of traditional models;
* Modal alignment effectiveness: Through TOT and codebook quantization, the distribution differences of heterogeneous data are significantly reduced;
* Engineering practicality: efficient memory management and parameter sensitivity, suitable for practical material design scenarios.

Paper address:
UniMate Mechanical Metamaterials Benchmark Dataset:
Dataset: The first benchmark dataset for mechanical metamaterials covering multiple tasks
To address the problem of lack of multimodal coverage in existing data, the UNIMATE team based on the topological structure of Lumpe & Stankovic (2021),The first unified dataset including three-dimensional topology, density conditions and mechanical properties was constructed, and 500 topological structures with no more than 20 nodes were screened from 17,087 original topologies.
For each topology, the research team randomly assigned three different edge radii and generated three different density conditions for each topology (linking the edge radius to the equivalent edge length formula).
For each topology-density pair, the research team divided the 3D structure into small cubic voxels and then applied homogenization simulations to calculate the homogenized mechanical properties of the structure, including Young's modulus, shear modulus, and Poisson's ratio.Finally, 1,500 data points were obtained (500 topologies, each with 3 densities and corresponding performance).
In order to further enhance the diversity of the dataset,The research team performed data augmentation on each data point.By rotating the topology and performance with the same random rotation angle, each data point is rotated 9 times, and finally the dataset contains 15,000 samples, covering low-density (ρ=0.1) to medium-density (ρ=0.5) scenarios, and the topology satisfies cubic symmetry and periodicity.
Model architecture: modality alignment module and collaborative diffusion generation module
The UNIMATE model architecture is designed to solve the unified modeling problem of the three major modes of 3D topology, density condition and mechanical property in mechanical metamaterial design.Its core consists of the Modality Alignment Module and the Synergetic Diffusion Generation Module.As shown in the figure below, multi-task collaborative processing is achieved through training and reasoning processes.

Modality Alignment Module: Unifying Multimodal Latent Spaces
The goal of this module is to map three heterogeneous modalities (topology, density, mechanical properties) into a shared discrete latent space.Tripartite Optimal Transport (TOT) is used to align modal distributions, narrow inter-modal differences, and address data complexity challenges.
Specifically, inspired by VQ-VAE, this module first maps the raw data into a discrete latent space. For the 3D topology, a graph convolutional network (GCN) is used as an encoder to convert the node coordinates and adjacency matrix of the topology into latent embeddings; for the density condition and mechanical properties, a multi-layer perceptron (MLP) is used as an encoder, respectively.
Then, a codebook is introduced to "round" the potential token, that is, find the closest prototype token in the codebook and replace the potential token with the prototype token. This can map the three different modalities to a shared discrete space consisting of a series of tokens.
In order to align the three modalities, the research team extended the optimal transfer (OT) to the three-party optimal transfer (TOT), and optimized the distribution of potential tokens by minimizing the three-party Wasserstein distance (TWD), thereby achieving the alignment of the three modalities. The design of the alignment loss function comprehensively considers factors such as reconstruction error, token rounding error, and modality alignment error.
Co-diffusion generation module: flexible handling of multiple tasks
The collaborative diffusion generation module is based on a score-based diffusion model. It uses modality-aligned tokens to complete the generation of unknown modalities, supports flexible conditional generation, and copes with the challenges of task diversity.
The input of this module is the "rounded" latent mechanical metamaterial (LMTR), in which some tokens are added with noise and regarded as unknown tokens. The diffusion process completes the generation of unknown tokens through a series of denoising steps, each of which uses Transformer as the backbone network.
In order to keep the given context token unchanged, the Transformer backbone network performs a partially frozen diffusion operation, that is, for the known tokens in the output, they are replaced with their initial values. This partial freezing process enables the model to process token sequences of arbitrary lengths and set any subset of tokens to unknown. Known tokens provide contextual information for other tokens, especially in the attention operation of the Transformer.
The generation loss function is defined as the distance between the rounded LMTR and the LMTR generated by diffusion, and the generation process is optimized by minimizing this loss function.
During the training phase, modality alignment and collaborative diffusion training are performed alternately. First, the original data is mapped to potential tokens through the encoder and codebook, and the modalities are aligned using TOT. Then, noise is added to the random modalities, and denoising training is performed through the diffusion model to optimize the overall loss.
In the inference phase, given some modal data (such as density and performance), the corresponding encoder generates known potential tokens, and the unknown tokens are initialized through the transmission plan TransPlan (high probability tokens are prioritized). The complete potential token sequence is then generated through the diffusion model, and finally reconstructed into the original modal data by the decoder.
Experimental conclusion: The performance of the three major tasks is comprehensively improved
Effectiveness Analysis
To verify the effectiveness of the UNIMATE model, the research team conducted comprehensive experiments and compared it with multiple baseline models on three tasks: topology generation, performance prediction, and condition confirmation.
In the topology generation task,F of UNIMATEqua and Fcond The indicators reached 2.74×10⁻² and 7.81×10⁻² respectively, which is 80.2% higher than the second-best baseline model SyMat. This means that the generated topological structure is closer to the engineering practical standards in key geometric features such as symmetry and periodicity.
In the performance prediction task,NRMSE of UNIMATEpp It is 2.44×10⁻², which is 5.1% higher than the second-ranked model.
In the condition confirmation task,NRMSE of UNIMATEcc The weight of the structure is 4.43×10⁻², which is 50.2% higher than the second-best model. In addition, UNIMATE can help engineers determine the optimal density for a given topology and performance requirements, and can reduce the weight of the structure by more than 30% while ensuring performance.
Time and space efficiency
In terms of time efficiency, we train each model and record the average time to process each batch. The results show thatThe batch processing time of each model is roughly linear with the batch size.As shown in the figure below, the slope of the UNIMATE model is at a moderate level, indicating that it has a moderate level of time efficiency.

In terms of space efficiency, many baseline models will trigger errors at smaller batch sizes due to insufficient GPU memory.The UNIMATE model is even batch No errors were triggered at a size of 10,000, showing that it is much more space efficient than other models.
Parameter Sensitivity
The research team also studied the model's parameter sensitivity to the latent token dimension d and the number of tokens in the codebook n. The experimental results are shown in the figure below.As the latent token dimension increases and the codebook size increases, the model performance generally improves.

Case Studies
To demonstrate the practical application of the UNIMATE model, the research team conducted a case study on topology generation for high stiffness and low density (HSLD) metamaterials. When training the model, the metamaterial data that exhibited better HSLD properties were selected from the original dataset, the density condition was restricted to a lower value (such as 0.3), and the required stiffness was adjusted within a certain range (such as 0.1 to 0.5).
The experimental results show thatThe UNIMATE model is able to generate a series of topological transitions that vary with performance.In the HSLD target task, the model suggests the use of the octet truss topology, which is a known high-stiffness topology candidate. In addition, the model is able to generate novel intermediate topologies that are not included in the training dataset.This suggests its potential to approximate intermediate transitions within a given distribution and enable the proposal of novel metamaterial candidates with desired properties.
Empowered by machine learning algorithms, a new journey in mechanical metamaterial design begins
With the deep involvement of machine learning, the inherent paradigm of mechanical metamaterial design is being rewritten. In the field of academic research, the research on mechanical metamaterials continues to heat up. Scholars are gradually solving the challenges of high-degree-of-freedom metamaterial design, such as large amount of calculation, difficulty in observation and representation due to complexity, and numerous design space parameters by mining the complex relationship between material structure data and performance parameters and combining the nonlinear fitting ability of neural networks.
For example, a team from Pennsylvania State University in the United States proposed introducing a novel fixed attention mechanism into the deep learning framework to solve the computational challenges of metamaterial design. The metamaterial consists of two gold nanorods embedded in a dielectric substrate, and its structure is described by 12 parameters.The experiment used Lumerical FDTD simulation to generate 6,493 sets of data to train the network.The results show that compared with the network without attention mechanism, the prediction accuracy of this method is improved by 48.09%, the mean square error of the test set is 2.17×10⁻³, and the calculation speed is greatly improved. In addition, this framework can also be applied to the reverse design of plasma metamaterials, significantly reducing the computational cost and paving the way for efficient and real-time optimization of complex nanostructures.
* Paper address:
https://arxiv.org/abs/2504.00203
At the same time, the Atlantic University team proposed a new metamaterial observation device based on artificial intelligence, combining modern imaging hardware with cutting-edge machine learning algorithms. Compared with traditional observation techniques,The system offers significant improvements in accuracy, speed and the ability to detect elements that were hitherto undetectable.The results show that AI-driven methods not only improve the ability to define known metamaterials, but also open up new ways to find unique properties and behaviors, thereby accelerating the speed of invention in materials science and engineering. The relevant research has been selected for the International Journal of Futuristic Innovation in Engineering, Science and Technology (IJFIEST).
* Paper address:
https://journal.inence.org/index.php/ijfiest/article/view/369
In addition, a team from Seoul National University and others proposed a parameter-free design strategy for three-dimensional mechanical metamaterials, which uses a deep generative network based on point clouds to build a metamaterial structure library to train machine learning models.The trained latent space forms topological clusters of units with similar properties, enabling efficient exploration and smooth interpolation.In addition, the method can predict mechanical properties faster than traditional methods. The method creates metamaterials with targeted properties, unconstrained by parameterization constraints. Computational and experimental validation confirms that the expected properties are consistent within an acceptable error range.
* Paper address:
https://arxiv.org/abs/2411.19681
It is foreseeable that machine learning algorithms are pushing the design and application of mechanical metamaterials to new heights. With the continuous iteration of algorithms such as reinforcement learning and generative adversarial networks, machine learning is expected to bring more disruptive breakthroughs to the field of mechanical metamaterials and help it be widely used in more fields.
Reference Links:
https://mp.weixin.qq.com/s/-LTTHsvIz-x9p0zjT6I1kg
https://arxiv.org/abs/2411.19681
https://arxiv.org/abs/2504.00203